When Steve P arrived at GIBY with his recently acquired Westerly 57, he filled out a Winter Storage & Work Order form and checked off boxes for services he wanted performed on his new boat. One of the boxes he checked was for a Rig Inspection. Not a bad idea for a large sailboat, under new ownership, if only for peace of mind.
When the rig survey was complete, Steve received a thorough report from the GIBY rigging department. One of the identified areas of concern was at the gooseneck of his KZ Marine Leisure Furl boom. There was a crack, possibly superficial, but maybe not…
“Because the crack was at the gooseneck, a high load part of the rig, we recommended that the owner authorize disassembly and further inspection of the area,” says GIBY rigger, Doug. “Upon closer inspection, an old (failed) repair was discovered.”
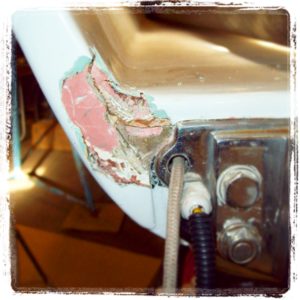
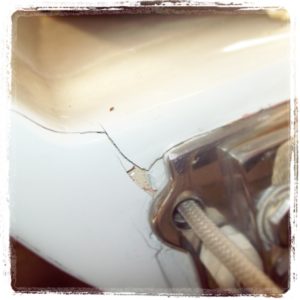
Since the composite boom was no longer supported by its manufacturer, GIBY offered to engineer a solution. Relying on the team’s depth of experience, the GIBY crew executed a fix using modern composite technology.
“The first step was to cut away the poorly manufactured areas and get down to good, stable material,” explains Operations Manager, Trevor.
GIBY glassman, Matt H, ground back the filler and fiberglass that had been used in the original repair and then rebuilt the damaged area using Pro-Set and a G-10 backing plate for reinforcement.
“Our repair allows for some flex,” explains Matt. “The materials we used aren’t brittle like the fiberglass tabbing that failed on the old repair. A bit of flexibility is much better for this application.”
But the shape of the boom, with natural voids behind the repair area, made the work somewhat complicated.
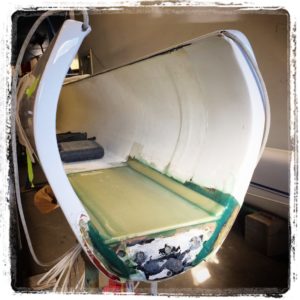
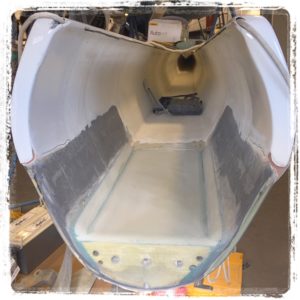
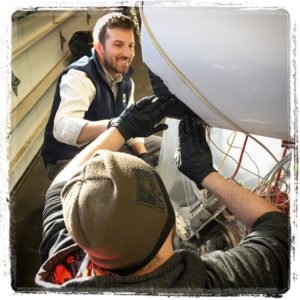
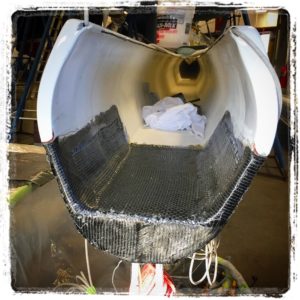
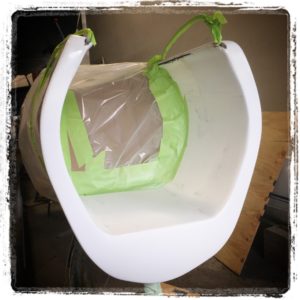
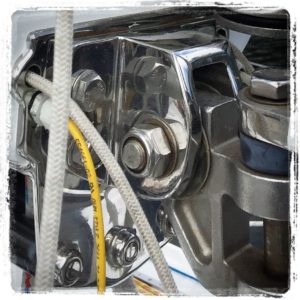
“We did a wet layup because the area was not conducive to vacuum bagging. We focused on controlling how much resin we applied to ensure consistency through the entire lamination,” explains Trevor.
For additional strength, the crew used carbon fiber cloth, which included a top layer of a 0/90 weave. After lightly filling and fairing the area, using Awlfair, all was primed and painted. Once the gooseneck was reassembled, the forward end of the boom was fit with a new stainless steel frame fabricated by GIBY’s rigger and metalsmith, John G.
“This type of repair is unusual for two reasons,” says Trevor. “One, it required that we engineer our own solution, as the boom was no longer supported by the New Zealand-based manufacturer; and, two, not many yards in our area work with carbon fiber. Our experience allowed us to do the work using modern materials and, through careful execution, give the owner a long-term fix we can stand behind.”
Leave a Reply